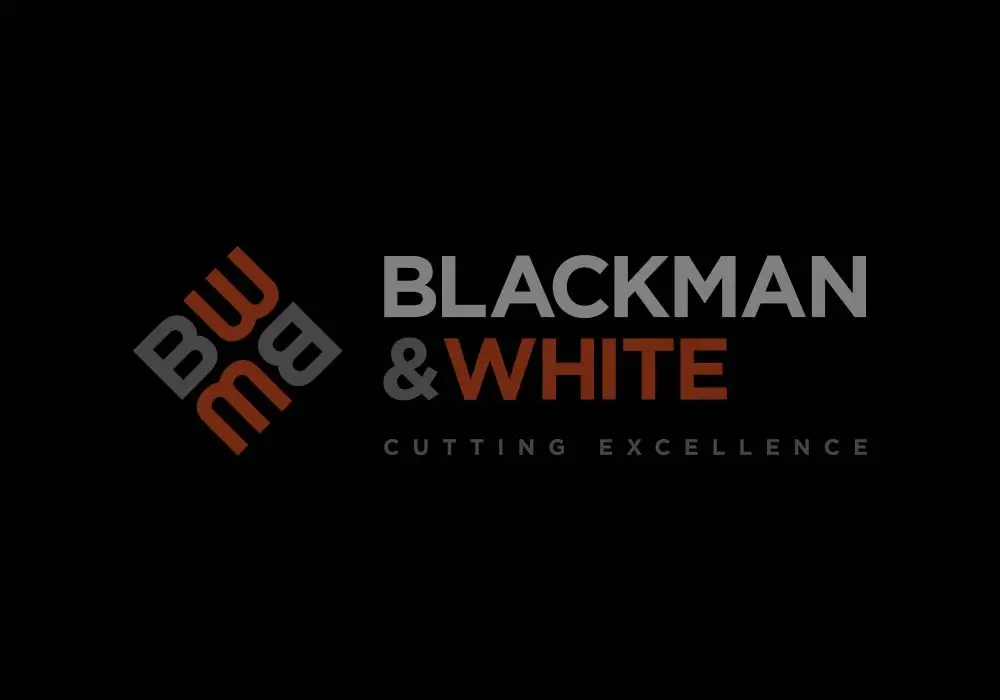
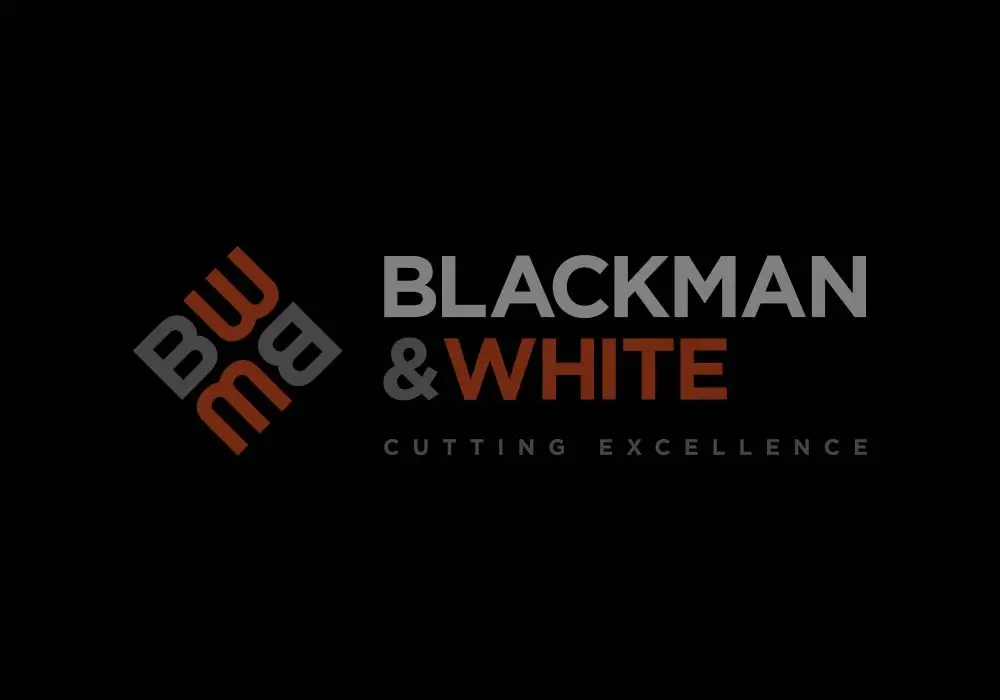
Pro Drive Cutting To Maximise Efficiency And Accuracy
By Blackman & White on February 9th, 2018
THE BRIEF
Prodrive designs and manufactures car body parts for motor racing and rallying, using specialist carbon composites. For years their car templates were cut by hand but they wanted to upgrade this time-consuming process which also allows human error and wastage of around 40%.
OUR SOLUTION
An automated cutter from the Orion range to deliver accuracy and reduce wastage.
THEIR VERDICT
Ian Hanscombe, composites manager for Prodrive, said: “Two years ago the composite shop was running at about 60% efficiency, mainly due to the time taken to manually cut patterns. Now that figure is between 86% and 92%.
“Everyone has bought into automated cutting and the guys appreciate that automation saves them time and they get a higher quality result so they’re far more motivated.
“Thanks to the BW Orion machine we have halved our material wastage – automating the cutting process really is a no-brainer for anybody working in composites.”
THE TECHNICAL SPECIFICATION
To simplify and standardise the cutting process we developed a bespoke software programme to run a fully automated Orion cutter. Operatives simply select the pattern, load the material and the machine does the rest. The software can calculate the most economical use of the material, even taking into account the weave of the fabric. This maximises the strength of the finished item. Prodrive estimates savings in wastage alone cover the cost of the machine.